Navigating the World of Fasteners and Machining: Methods for Accuracy and Rate
In the detailed realm of fasteners and machining, the mission for precision and rate is a perpetual obstacle that demands thorough attention to detail and strategic planning. From recognizing the varied array of bolt kinds to selecting ideal products that can withstand rigorous demands, each step in the procedure plays an essential function in attaining the preferred end result.
Understanding Bolt Types
When choosing bolts for a job, recognizing the different types offered is crucial for making sure optimal efficiency and integrity. Bolts are utilized with nuts to hold products together, while screws are versatile fasteners that can be utilized with or without a nut, depending on the application. Washing machines are essential for distributing the tons of the fastener and protecting against damages to the product being fastened.
Choosing the Right Products
Recognizing the relevance of choosing the appropriate products is critical in guaranteeing the optimal efficiency and integrity of the picked fastener kinds reviewed formerly. When it involves fasteners and machining applications, the material selection plays a critical function in determining the total toughness, resilience, deterioration resistance, and compatibility with the designated setting. Various materials use differing homes that can substantially impact the performance of the fasteners.
Usual products utilized for fasteners consist of steel, stainless steel, light weight aluminum, titanium, and brass, each having its unique strengths and weaknesses. Steel is renowned for its high stamina and resilience, making it suitable for a broad range of applications. Selecting the best product includes considering elements such as strength requirements, ecological problems, and budget plan constraints to ensure the wanted performance and longevity of the bolts.
Precision Machining Techniques
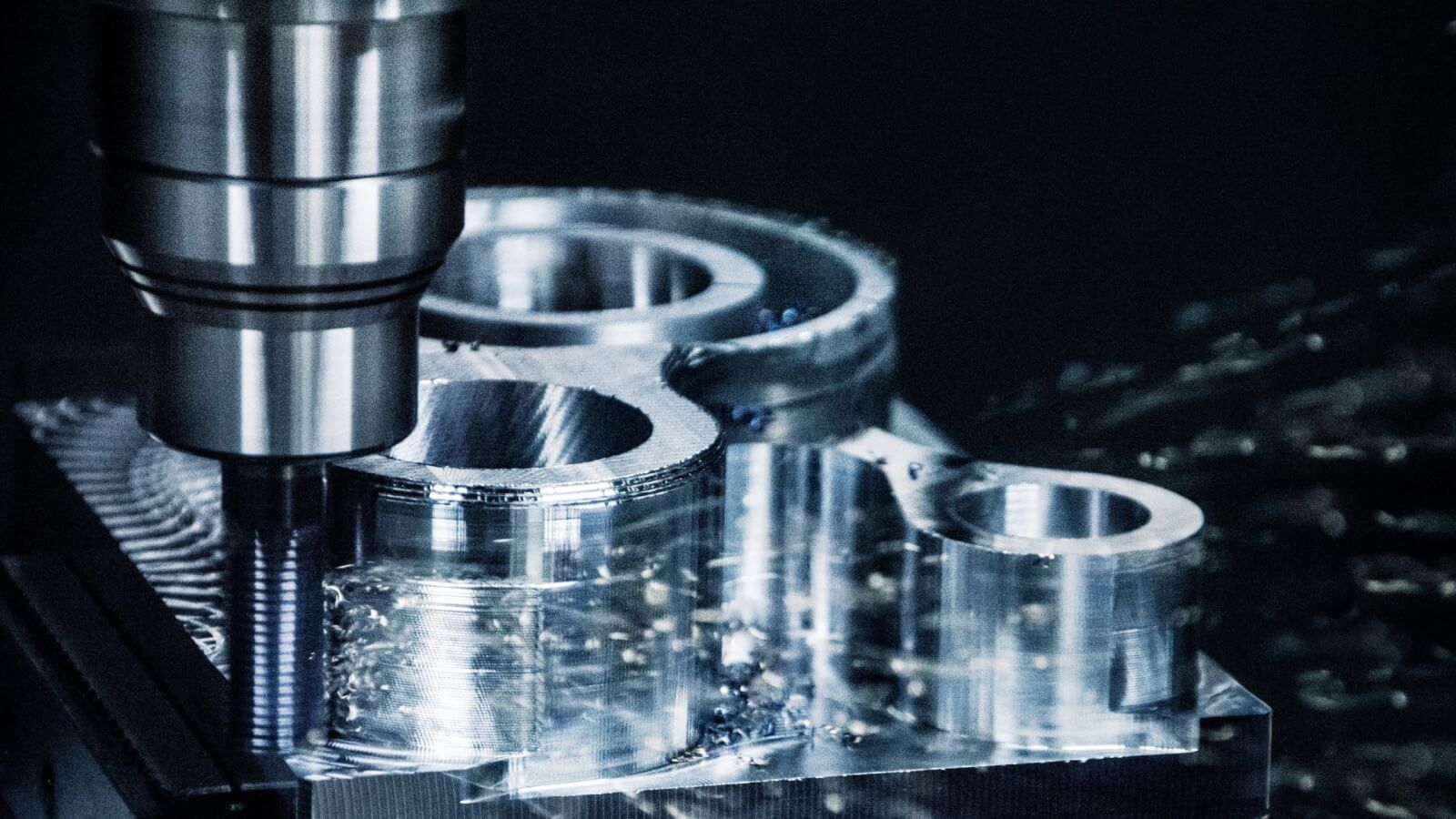
In addition to CNC machining, various click to find out more other accuracy techniques like grinding, transforming, milling, and drilling play crucial i was reading this roles in bolt production. Grinding aids accomplish great surface finishes and limited dimensional tolerances, while turning is often utilized to develop cylindrical components with precise diameters. Milling and boring procedures are essential for shaping and developing holes in fasteners, guaranteeing they fulfill exact specs and feature appropriately.
Enhancing Speed and Effectiveness
To enhance bolt production processes, it is essential to enhance operations and apply effective strategies that match accuracy machining methods. Automated systems can handle recurring tasks with precision and rate, enabling employees to focus on even more complex and value-added tasks. By combining these methods, makers can achieve an equilibrium between speed and accuracy, ultimately enhancing their affordable edge in the fastener sector.
Quality Assurance Actions
Executing extensive quality assurance steps is critical in guaranteeing the integrity and uniformity of fastener items in the production procedure. Quality control procedures include numerous phases, starting from the selection of resources to the final inspection of the finished bolts. One basic aspect of high quality control is performing extensive product inspections to verify compliance with specs. This entails analyzing variables such as material make-up, resilience, and strength to guarantee that the fasteners satisfy market criteria. Additionally, keeping track of the machining processes is necessary to maintain dimensional accuracy and surface area coating top quality. Utilizing advanced innovation, such as automated examination systems and accuracy measuring devices, can improve the accuracy and efficiency of quality control treatments.
Routine calibration of equipment and equipment is imperative to maintain uniformity in manufacturing and make certain that bolts meet the needed resistances. Applying stringent procedures for recognizing and attending to flaws or non-conformities is essential in protecting against substandard important source items from entering the market. By establishing a comprehensive quality assurance structure, producers can maintain the reputation of their brand and provide bolts that fulfill the greatest criteria of efficiency and longevity.
Final Thought

In the intricate world of bolts and machining, the mission for precision and speed is a perpetual obstacle that requires meticulous attention to detail and strategic planning. When it comes to bolts and machining applications, the product option plays a crucial role in identifying the overall strength, resilience, corrosion resistance, and compatibility with the intended environment. Precision machining entails numerous advanced methods that ensure the limited resistances and specs required for fasteners.In addition to CNC machining, various other precision strategies like grinding, transforming, milling, and exploration play important roles in bolt manufacturing.To enhance fastener production processes, it is vital to simplify procedures and execute efficient strategies that complement precision machining methods.